座繰り穴の加工
座繰り穴を加工する方法としては
- エンドミルで回す
- 座繰り径のエンドミルで突く
- 先端をフラットに研いだドリルで突く
- 座繰り用の段付きドリルで座繰る
今まではこの4つで加工していました。
エンドミルで回す以外は、研いだり専用工具増やしたりで選択肢には入れたくありません。
エンドミルで回す方法は、座繰り穴より小径を使うし、
時間もかかるので改善は必要だなと考えていました。
座繰りは主に下の図面のようなシチュエーション多い。
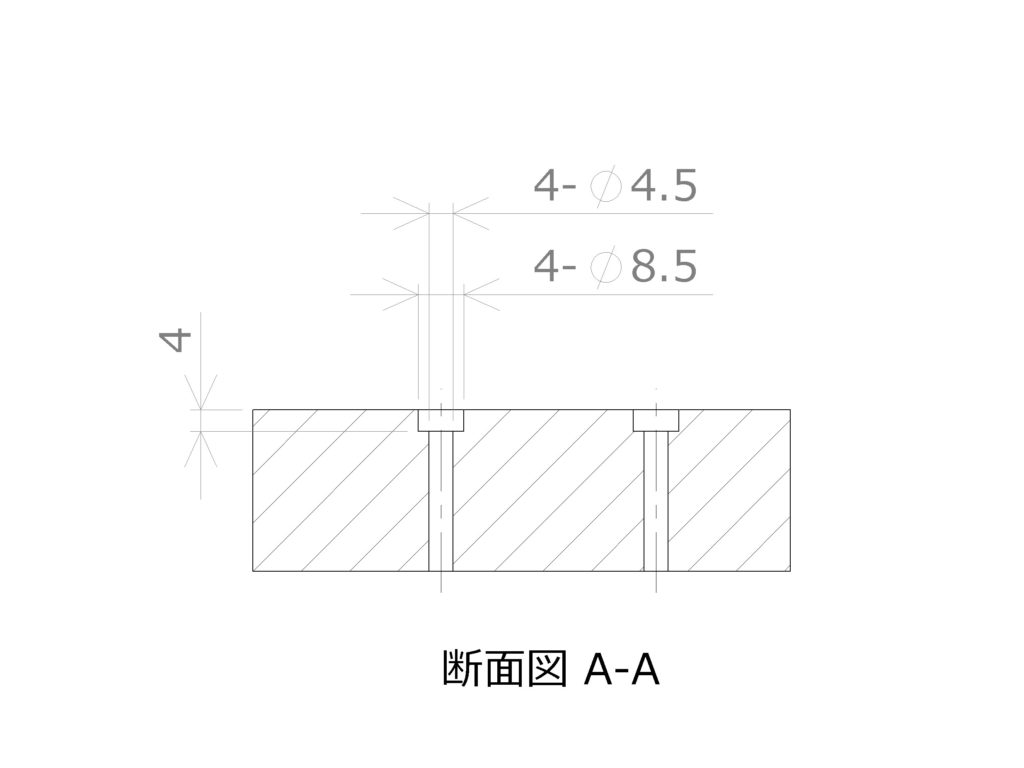
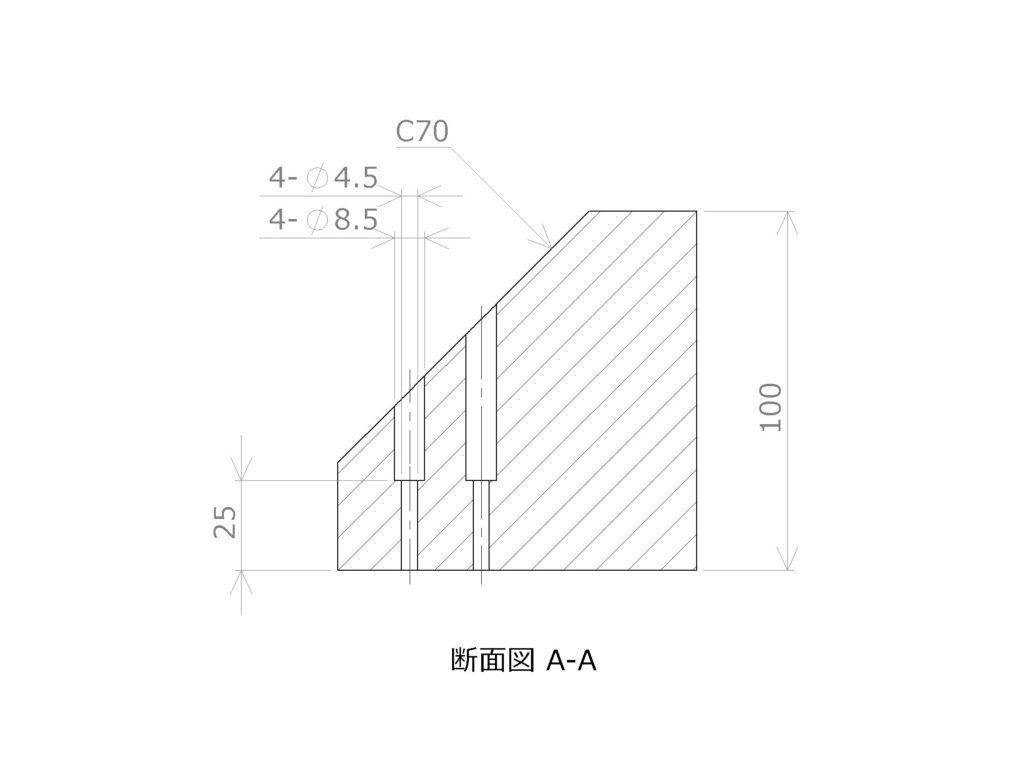
傾斜面に座繰りがある場合は、以下の順です。
- エンドミルで穴径+0.02程度の座面を作る
- センタリングするか、ドリルで穴あけ
- 段付きの場合は先に大径
- 小径穴あけ
座面を作るときは、次に使用するドリル径ができるまで深く座繰ります
傾斜面で座面が欠けないように注意すること
下穴が先か、座繰りが先か
段付き穴やバカ穴と座繰りの組み合わせで、どちらを先にあけるかという問題に差し掛かる場合があります。
ボクが機械加工を始めたころは、下穴をあけて段階的にあなを広げると教わりました。
たとえばこちらの図面のような段付き穴があるとします。
Φ10とΦ20、正しい加工の順番はどちらをが先でしょうか?
- Φ10ドリル→Φ20ドリル
- Φ20ドリル→Φ10ドリル
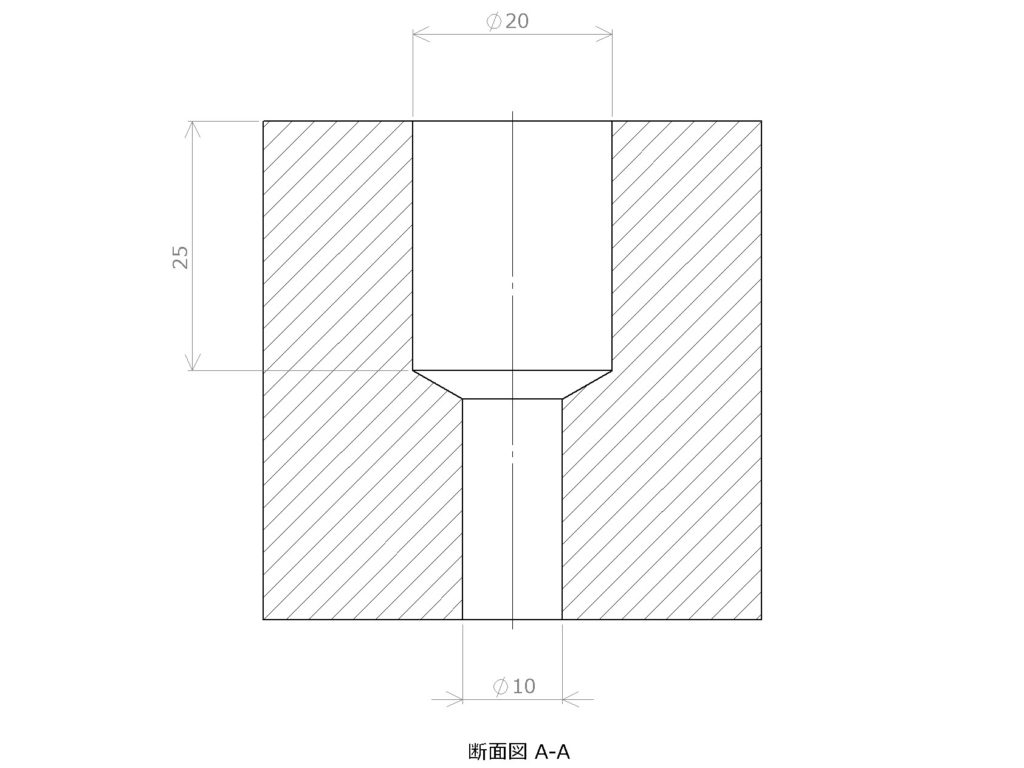
①が正しいという方が多いのではないでしょうか。
答えは②です。
マシニングセンターで加工する場合は問答無用で②です。
①で加工経験のある方ならお分かりだと思いますが、切粉の状態が最悪ですよね。
ドリルの肩付近のみで切削されたカールせず長い切粉がびろ~んと出てきます。
マシニングをはじめNC加工では恥ずかしい切粉です。
ワークや機械に巻き付き「チョコ停」の原因です。
フライスなどの汎用機なら切粉を除去しながら加工できますが、危ないし効率は最悪です。
ドリルメーカーは各社研究を重ね、最適に切粉を分断するドリル先端形状にしているのです。
あとから大径ドリルを入れた場合、求心力も失われているので精度も出ませんよね。
しかし、段付き穴のほとんどは大径底はフラットの座繰りです。
①の方法で段底のみエンドミルで加工するのも有りですが、工具本数が増えます。
そこで、平面・傾斜面に大径→小径の順番で加工でき、段底がフラットで、工具2本で済むのが、
フラットドリルなのです
外観
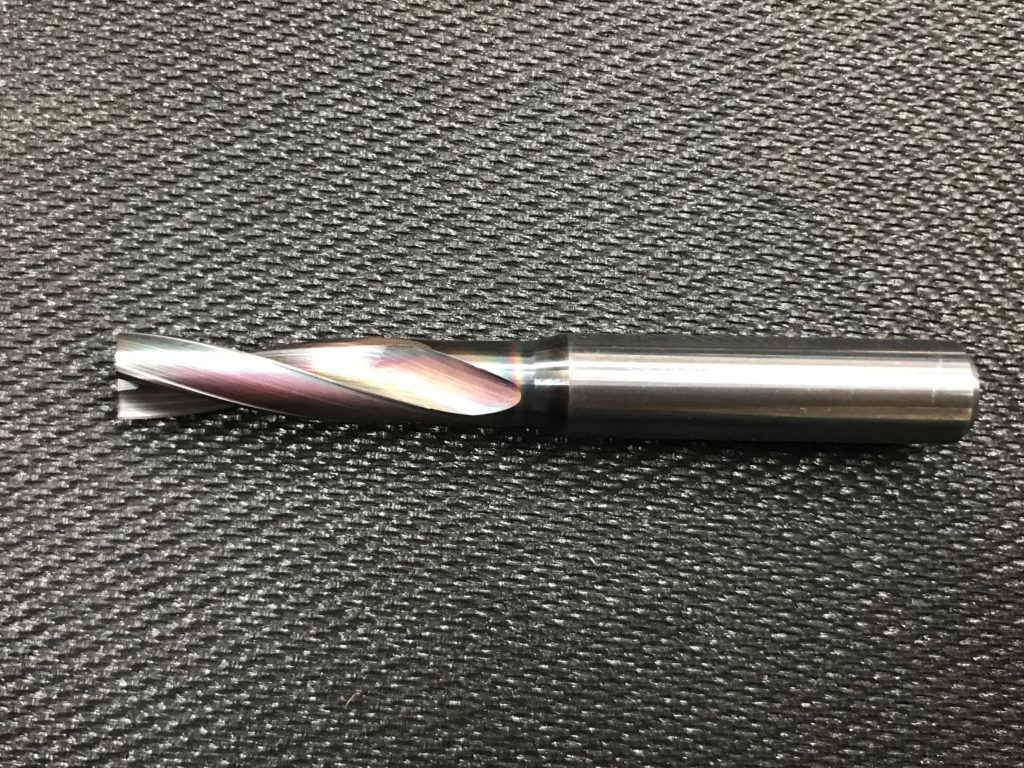
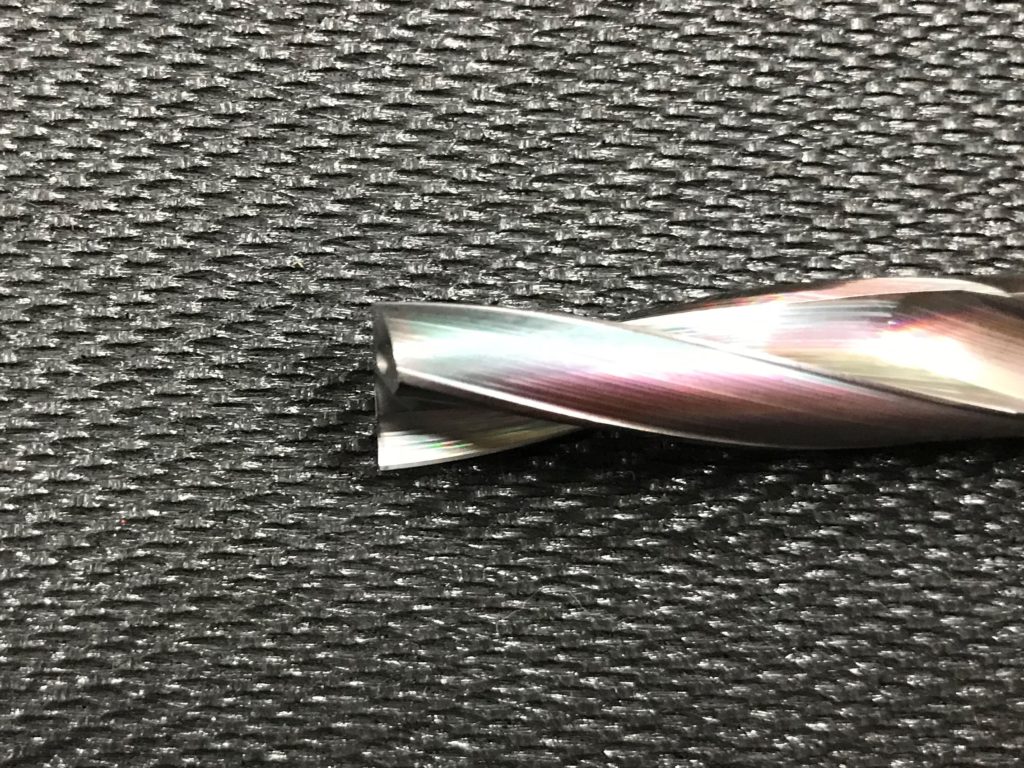
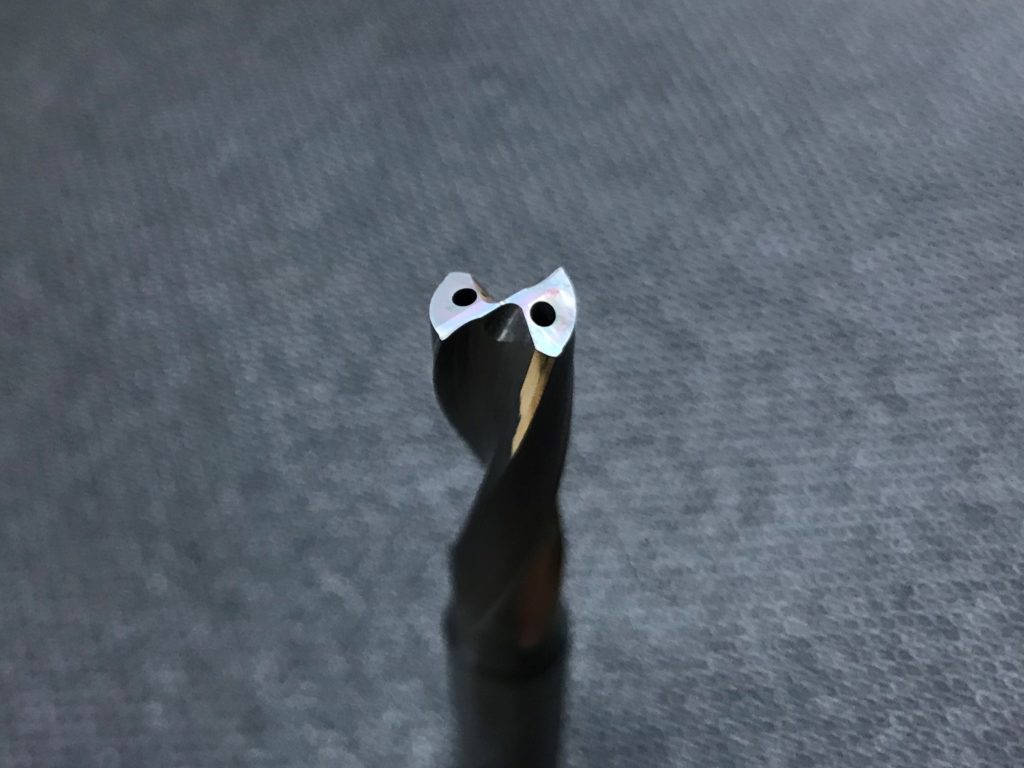
使い方
参考工具
メーカー:OSG
型番:ADFO 3D 8.5
サイズ:Φ8.5
こちらは油穴付き、
スピンドルスルークーラント搭載機械であれば効率的に加工点を冷却・潤滑できます。
高圧クーラントであれば、強制的に切粉を輩出可能なので、
仕上げ面向上とノンステップ加工も余裕です。
エンドミルのように刃底角度が無いので、加工面は文字通りフラット、
次工具がドリルでも、センタリング不要です。
ツールホルダーは必ず高精度で合成あるミーリングチャックかコレットチャック使用してください。
まとめ
- 段付き穴は大径→小径の順
- 座繰り穴はフラットドリル
- 傾斜面の穴あけはフラットドリル
- 良い切粉は分断されたパラパラ状態
ドリルや穴あけに関するオススメの書籍はこちら